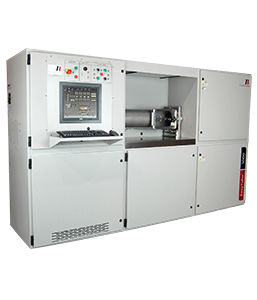
The EasyTube 3000 system is the most advanced customizable chemical vapor deposition/annealing process tool for nanomaterials synthesis, thin film depositions and anneals.
EasyTube® 3000 is capable of synthesizing a myriad of nanostructures and thin film including single-walled or multi-walled nanotubes, Graphene, nanowires such as Si, Ge, ZnO, GaN, BN, and thin film such as Si, SiO2 and Si3N4 using selected combinations of hydrides, liquids and/or solid precursors.
The system can safely process most pyrophoric and toxic chemicals including silane, germane, diborane, phosphine, HCl, and metal organic precursors, etc.
The system has application configured safety protocols embedded into relay logic, PLC, and CVDWinPrC™ software.
EasyTube 3000EXT
The EasyTube® 3000EXT model has an extended frame size to accommodate larger system modules. These can include a glovebox, loadlock, a rolling furnace for rapid heating and cooling, an upstream RF plasma generator, and/or an option to increase the process chamber ID up to 200 mm to accommodate full 6” wafers.
STANDARD FEATURES
- CVDWinPrC™ system control software for realtime process control, data logging, and recipe editing.
- Preprogrammed process recipes.
- Substrate sizes up to 150 mm x 150 mm (batch processing of multiple wafers per run also possible).
- Cantilevered automatic substrate loading/unloading system.
- Up to 12 mass flow-controlled UHP gas lines.
- Atmospheric and/or low pressure process configurations available.
- 3-zone resistance furnace for temperatures up to 1200 °C or optional infrared/radio frequency induction heating.
- Proprietary realtime cascade process temperature control.
- High throughput with FastCool™ furnace.
- User ability to set warnings and alarms.
- Comprehensive software and hardware safety interlocks.
- 1 year warranty.
- On-site system startup and training.
- Semi – S2/S8 and CE Compliant.
OPTIONS
- High temperature resistance furnace up to > 1200 °C.
- Infrared heating for rapid thermal processing > 1100 °C.
- Radio frequency induction heating for process temperatures > 1500 °C.
- Upstream plasma.
- DC bias field assisted growth.
- Substrate rotation for improved process uniformity.
- Rectangular process tube for improved laminar gas flow.
- Liquid/solid source vapor delivery kit.
- Bubbler liquid auto refill.
- Run/vent: stabilizes gas flows (bypassing the process tube) before flowing into process tube.
- Loadlock to isolate the process tube from ambient atmosphere.
- Glovebox with exhausted N2 or Ar purge.
- High vacuum process chamber and/or loadlock chamber.
- Residual gas analyzer.
- Air to water heat exchanger for cooling water.
- EasyGas™ hazardous gas cabinets.
- EasyPanel™ UHP gas panels for argon, nitrogen, helium, oxygen.
- EasyExhaust™ exhaust gas conditioning system (scrubber/pyrolyzer).
FACILITY REQUIREMENTS
- Electrical* : 208 VAC, Fase 3, N, G 40 – 60 A.
- Dimensions* : 96″/ 119″ Length, 33″ Width, 70″ Height.
- Cabinet Exhaust* : 500 cfm.
- Cooling Water* : 2 gpm 50-75 psig.
- Pneumatic Supply : Clean DRY Air or N2 , 80 psig.
- Facility Nitrogen* : 20 slpm 20 psig.
- Process Gases : Customer specified.
- *NOTE : Electrical varies with country, Facility requirements vary with system options, Consult Factory for details.